The Diesel cycle is the thermodynamic cycle which approximates the pressure and volume of the combustion chamber of the Diesel engine, invented by Rudolph Diesel in 1897. It is assumed to have constant pressure during the first part of the "combustion" phase , v2 to v3 in the diagram .
Maximum thermal efficiency
The maximum thermal efficiency of a diesel cycle is dependent on the compression ratio and the cut-off ratio. It has the following formula:

Where
- ηth is thermal efficiency
- α is the cut-off ratio
(ratio between the end and start volume for the combustion phase) - r is the compression ratio

- γ is ratio of specific heats (Cp/Cv)
The cut-off ratio can be expressed in terms of temperature as shown below:



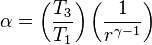
T3 can be approximated to the flame temperature of the fuel used. The flame temperature can be approximated to the adiabatic flame temperature of the fuel with corresponding air-to-fuel ratio and compression pressure, P3. T1 can be approximated to the inlet air temperature.
This formula only gives the ideal thermal efficiency. The actual thermal efficiency will be significantly lower due to heat and friction losses. The formula is more complex than the Otto cycle (petrol/gasoline engine) relation that has the following formula;

The additional complexity for the diesel formula comes around since the heat addition is at constant pressure and the heat rejection is at constant volume. The Otto cycle by comparison has both the heat addition and rejection at constant volume.
Comparing the two formulae it can be seen that for a given compression ratio (r), the ideal Otto cycle will be more efficient. However, a diesel engine will be more efficient overall since it will have the ability to operate at higher compression ratios. If a petrol engine were to have the same compression ratio, then knocking (self-ignition) would occur and this would severely reduce the efficiency, whereas in a diesel engine, the self ignition is the desired behavior. Additionally, both of these cycles are only idealizations, and the actual behavior does not divide as clearly or sharply. And the ideal Otto cycle formula stated above does not include throttling losses, which do not apply to diesel engines.
The Diesel cycle is a combustion process of a reciprocating internal combustion engine. In it, fuel is ignited by heat generated by compressing air in the combustion chamber, into which fuel is injected. This is in contrast to igniting it with a spark plug as in the Otto cycle (four-stroke/petrol) engine. Diesel engines (heat engines using the Diesel cycle) are used in automobiles, power generation, diesel-electric locomotives, and submarines.